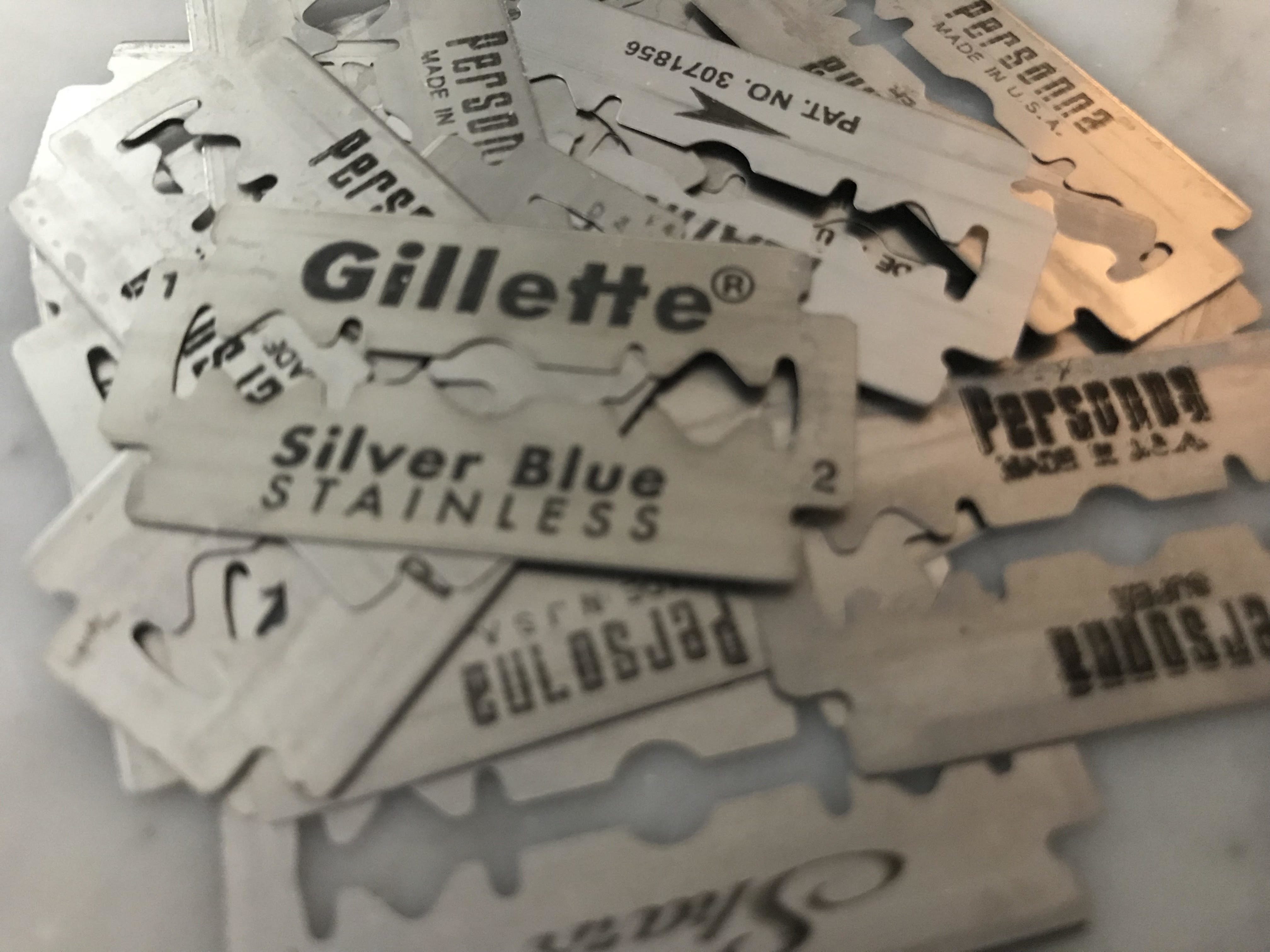
Double-edge razor blades all look really similar, but they are not homogeneous commodities like sugar or corn. In other words, they do have some distinguishable features that make each brand different.
They do however all share the same basic, fundamental design. Which is kind of important because if they didn’t all have the same basic size, shape and dimensions, you would be limited on which blades would actually fit and work in which razors.
And because they all have the same universal shape, design and fundamental features, there's not a lot of room for creativity in the manufacturing process.
There definitely are some manufacturing differences from brand to brand like composition quality of the metal they use or how the blade is sharpened and polished or what chemical coatings are applied. But the actual process of how DE blades are manufactured is pretty consistent.
The Manufacturing Process
The double-edge razor blade manufacturing process starts off with a strip of stainless steel that is hundreds of feet long. This strip of material is a metal composite, paper thin, extremely light and has dull edges.
The composite starts off very soft and flexible, so the first step is to harden it. The material is hardened through a process of progressively heating it up and then cooling it back down.
It depends on the manufacturer but it commonly takes around 4 rounds of heating and cooling to get the product to the optimal hardness. The end product blade needs to be nice and stiff, not flexible, so this is a really easy but important step in the process.
Once the product has reached the optimal hardness, it is then sent through a series of grinding and polishing machines. The purpose of the grinding machine is to sharpen the edges while the polishing machine cleans up the edges by removing any imperfections.
Both the grinding and polishing procedures are incredibly important. Grinding the edges is what makes the edges sharp so it will cut the hairs right off. The polishing step smooths out the edges by removing any burrs or stray fragments from the cutting edges. DE blades need to have sharp but smooth edges to ensure they can cut the hairs without cutting the skin. One feature without the other renders a blade unusable and possibly dangerous.
At this point in the manufacturing process, the product that started as a long, dull strip of soft metal is now thousands of sharp individual DE razor blades. They are not done yet though! Now they need to be coated and treated with a variety of lubricants and finishes.
The first coating applied is typically a chromium based coating. It is applied to the entire blade but is intended to ensure that the cutting edges stay hard and resistant.
Next, a non-stick coating is sprayed on. The last thing you want is for the blade to cause a lot of friction, you want the blade to just glide across your face. The non-stick coating helps reduce the amount of friction between your face and the blade which helps prevent skin irritation and razor burn.
Lastly, the blades are submerged into an oil-based solution that helps give it some added protection from corrosion. Corrosion is the primary contributor to blade deterioration. Blades typically only last 4 or 5 shaves, but any added protection from blade corrosion is always helpful.
We left out a lot of little steps in the manufacturing process like when the stainless steel gets cut into individual blades, when the brand logo gets applied, how they are packaged, etc. But we think this should give you a good overview of how the manufacturing process is simple and straightforward.
Key Takeaway: Not All DE Blades Are Created Equally
So what’s the key takeaway from all this? There’s not a lot of wiggle room in regards to different features, but that certainly doesn't mean all DE blades are the same.
Think back, what were some of the manufacturing steps that may affect the quality, sharpness and performance of the final product?
- How sharp of a grinder was used?
- What is the composition of the metal?
- What lubricants and protective coatings were applied?
- How fine was the polishing?
No, you're not going have to research answers to these questions just to find the right blade. But it should make you think. What should I looking for in a DE razor?
Not sure where to start when shopping for double edge razor blades? Our 10 best safety razor blades article has all the information you need to find the perfect de blade for your safety razor. Seriously, go check it out.